Technology
Process owner
We are the process owners for our production chain. We are capable of designing, carrying out and internally monitoring each stage of our process. All motorcycle components are critical, and the only way to guarantee their absolute quality is to conceive and manufacture them entirely on site, under our direct supervision.
That’s how Domino products are produced each day: conceived, designed, manufactured, and tested entirely in Italy, since 1951.
Domino is a proud standard bearer for the world of Made in Italy products.
Assemblies
Whether we're talking about cable operated or electronic Ride by wire throttle controls, adjustable brake and clutch levers, electrical devices, or hall effect quick shifter sensors, each product passes through our dedicated assembly lines, which are manned by highly experienced and reliable personnel. The electrical and electronic products are then meticulously checked by specifically designed machines, which record their relative data in order to allow process capability studies to be conducted.
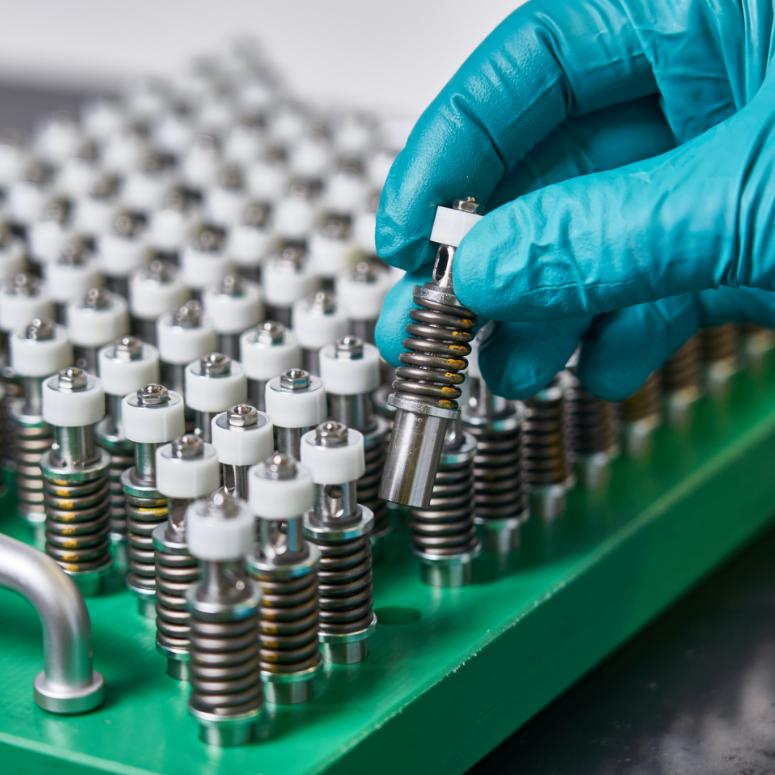
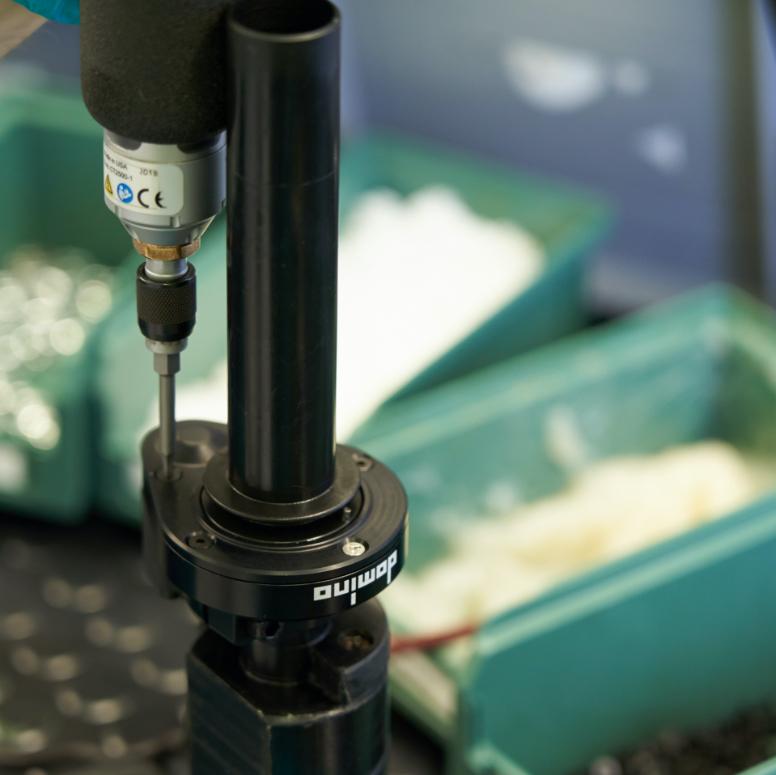
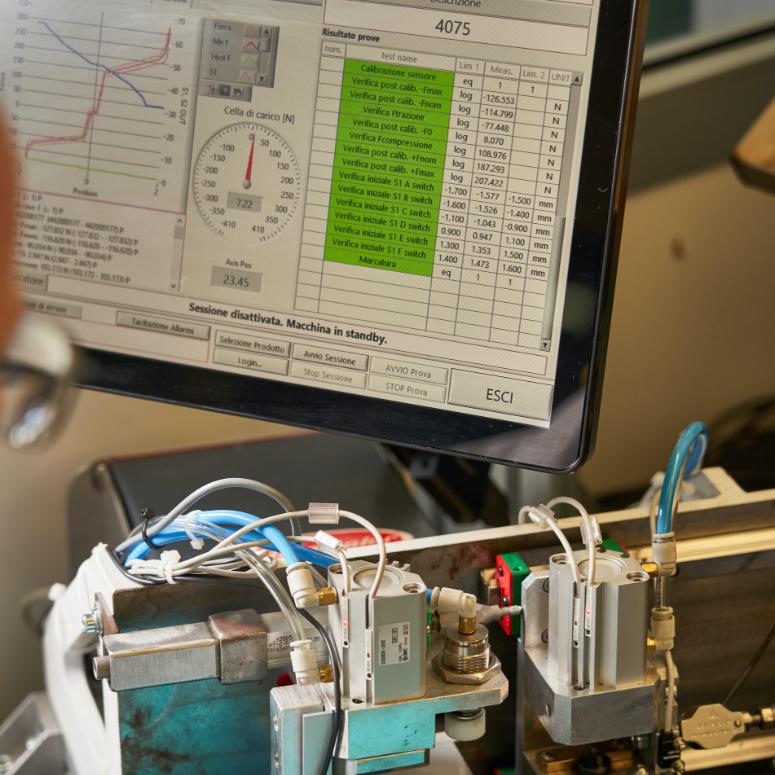
Aluminium die casting
Our automated moulding cycle consists of three islands manned by anthropomorphic robots, which handle everything from the melting furnace operations, to the de-moulding of the die-cast parts and the tumbling processes. The process is constantly controlled: from the quantometric chemical analysis of the molten aluminium bath, to the X-ray analysis of the casting with automatic CNC positioning, and the 100% selective control carried out by automatically weighing the pieces, all of which are useful for capability analyses.
Domino uses aluminium alloys compliant with the international standards, as well as special chemical compositions formulated according to its own specifications, derived from its seventy years of experience, which are designed to enhance the characteristics of its products.
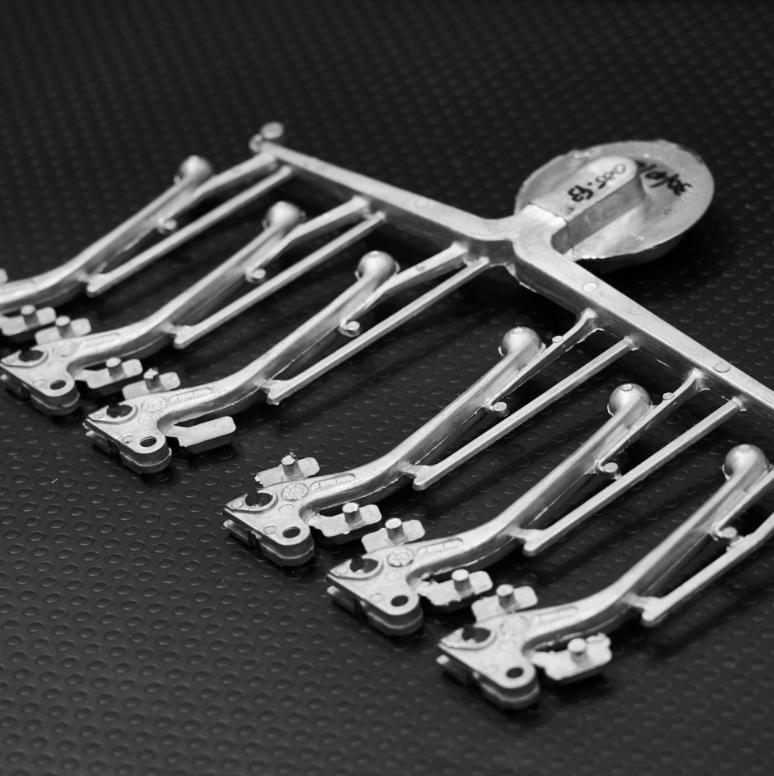
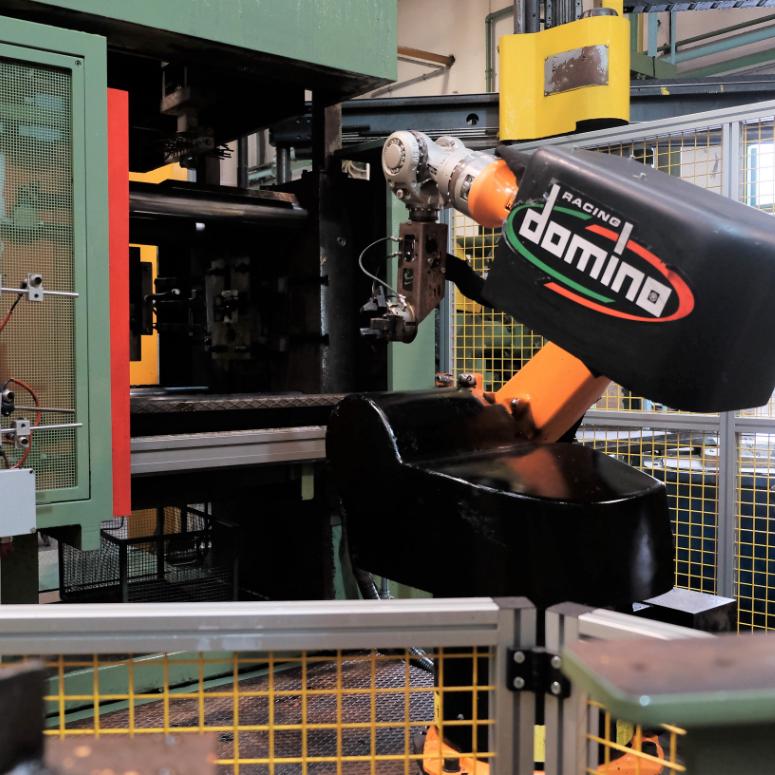
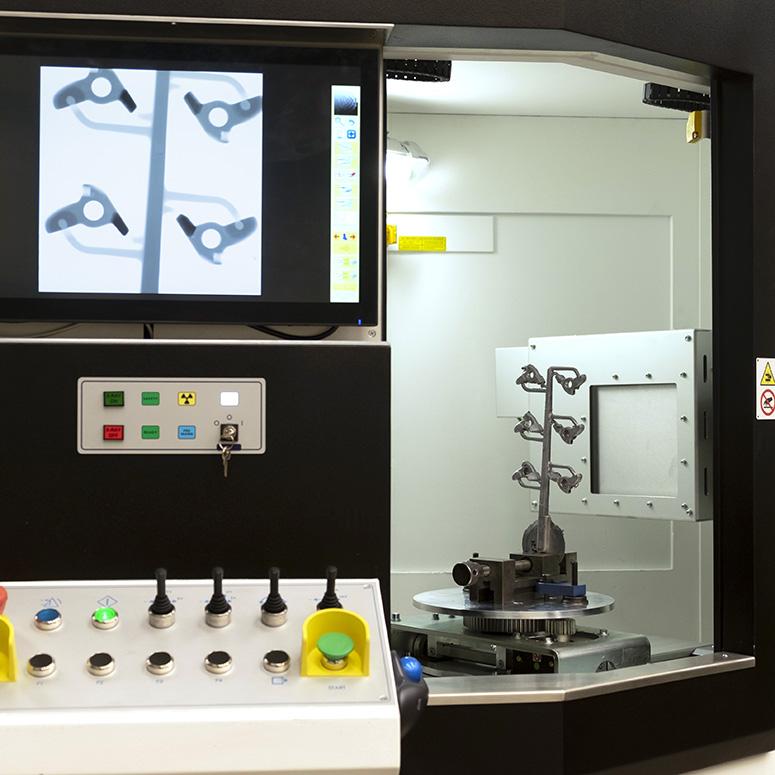
CNC machining
For a manufacturer of aluminium components, a large mechanical machining department is an absolute must. Among other things, this department features five three-axis numerical control machines with pallet changers, which are used to carry out specific processing operations, with minimal tolerance margins, on forged or die-cast pieces. This department processes all the die-cast and forged aluminium alloys, as well as ferrous-based materials for special Automotive products, and, in some cases, we even carry out third-party work based on specific customer designs.
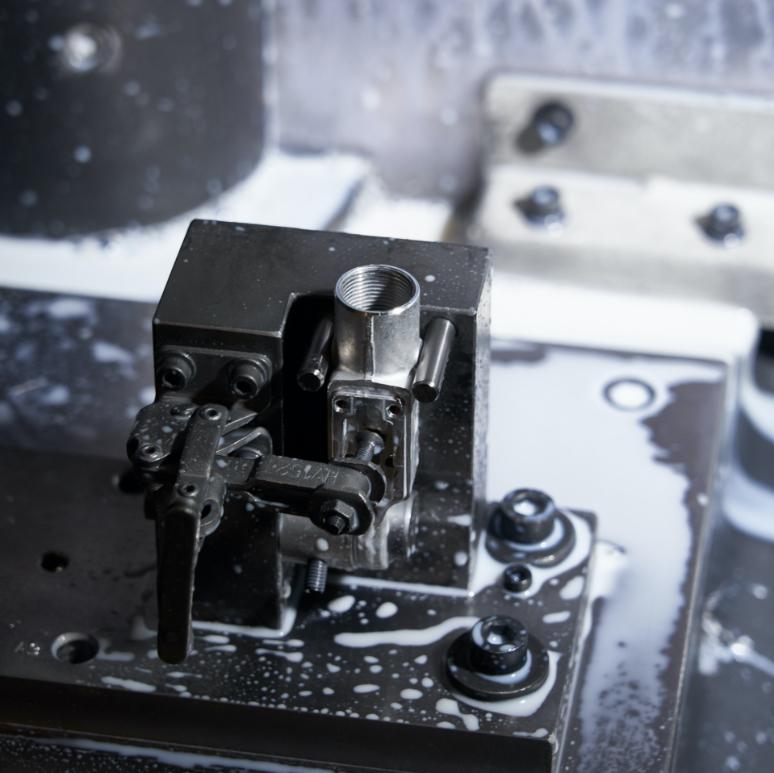
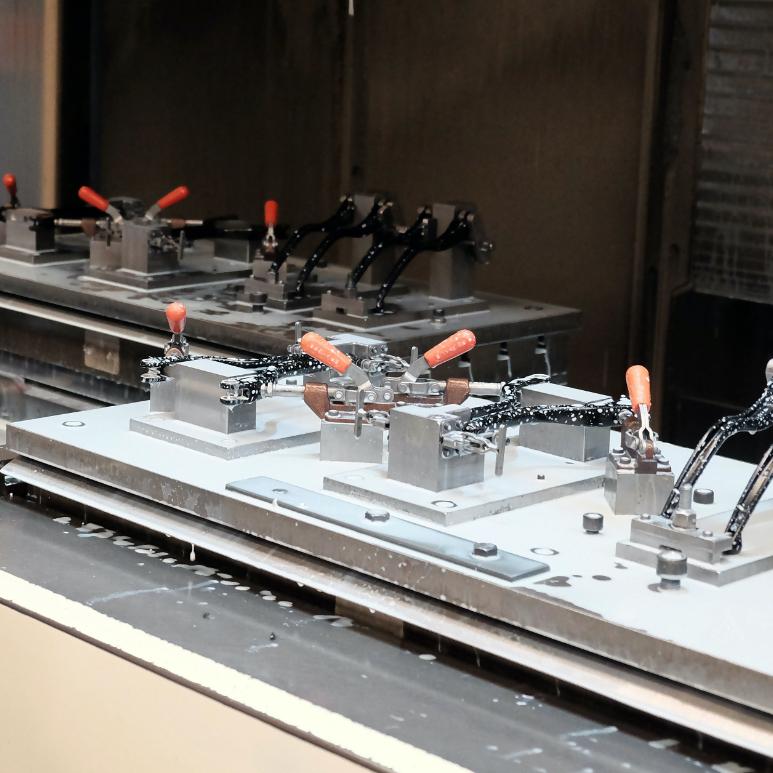
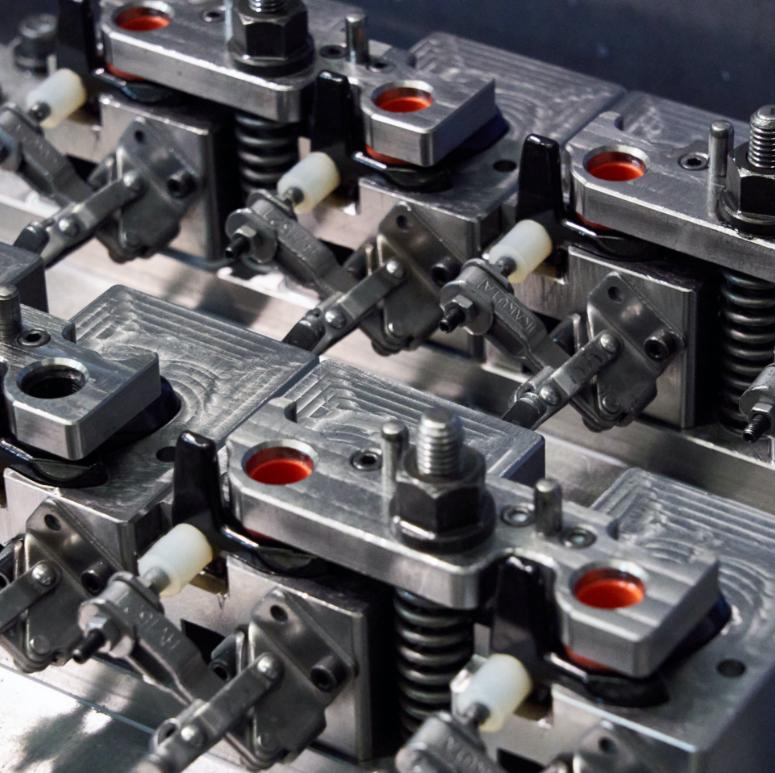
Plastic moulding
Our products are produced using 8 to 200 tonne injection moulding machines equipped with Cartesian robots for the introduction of threaded inserts and the extraction and palletization of the finished parts, or for the evacuation of the sprues. The processed materials range from thermoplastic elastomers, even co-moulded, to polymers loaded with talc, glass, and minerals.
These materials are validated in-house to ensure they meet a wide range of requirements: grip, wear, and environmental elements.
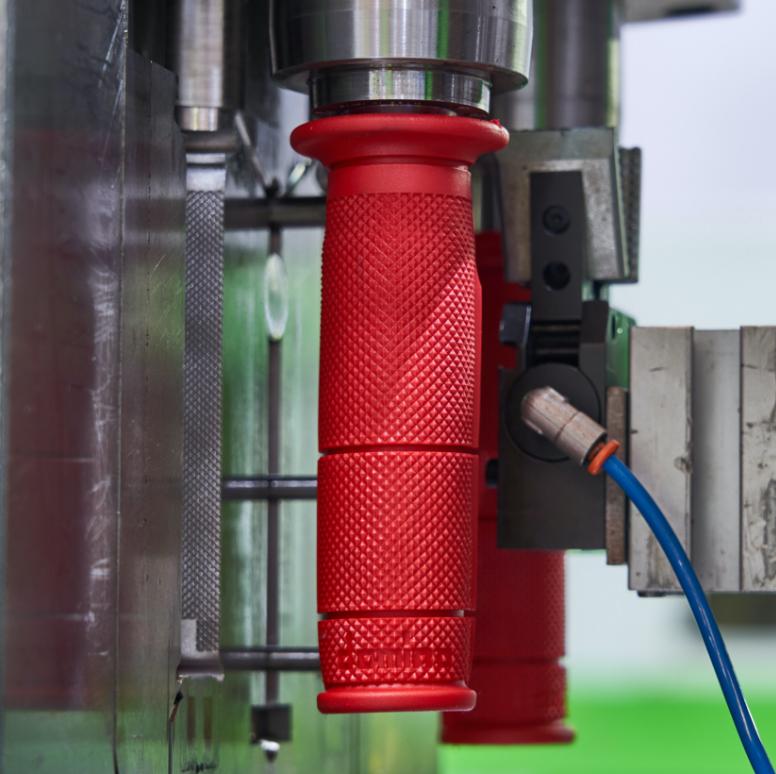
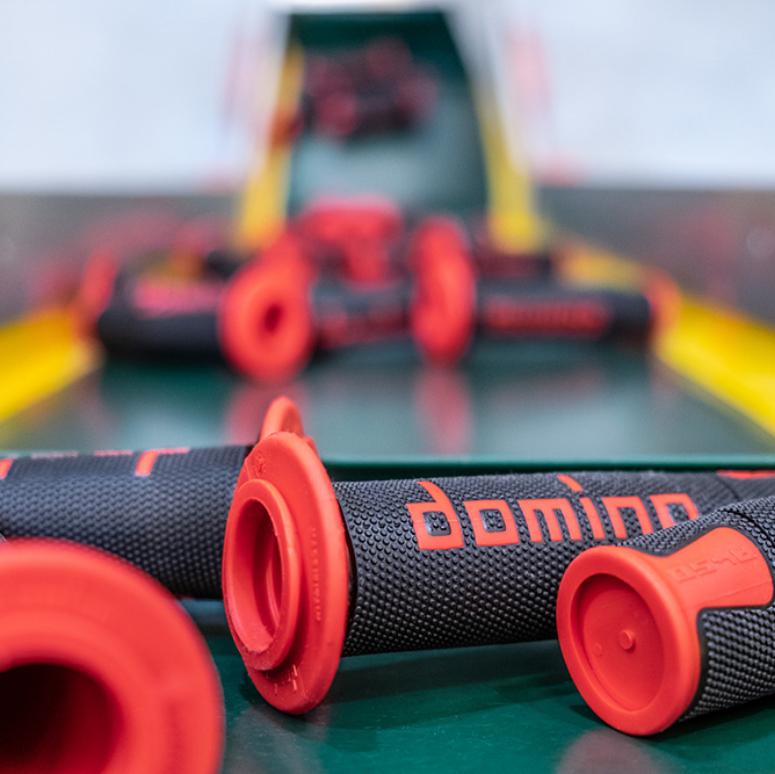
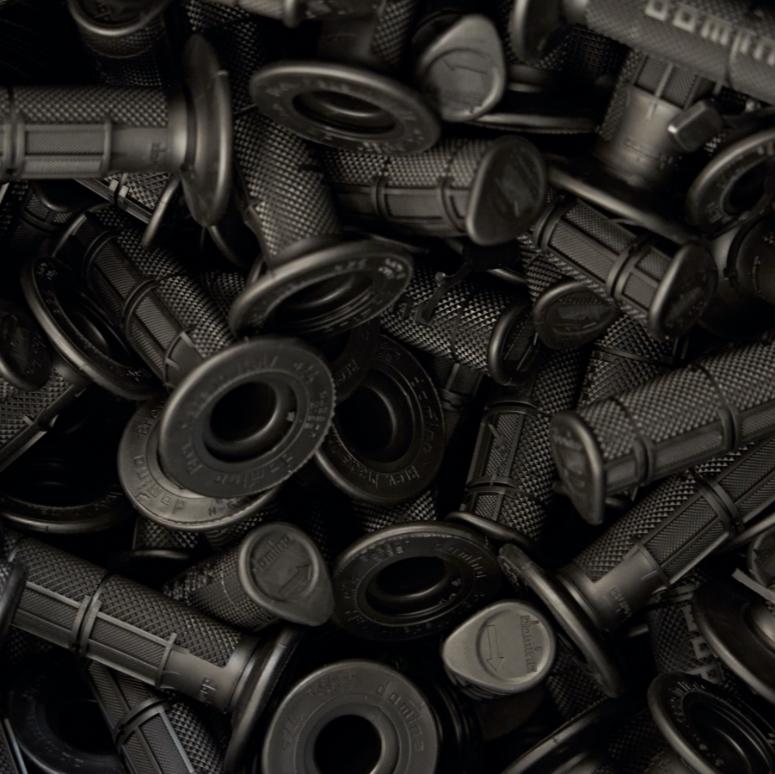
Handlebar Bending
The technological heart of the department consists of two CNC machines designed for bending steel or aluminium tubes, one with three axes and one with five axes, which are capable of transforming a simple unfinished tube into an actual motorcycle handlebar, entirely automatically.
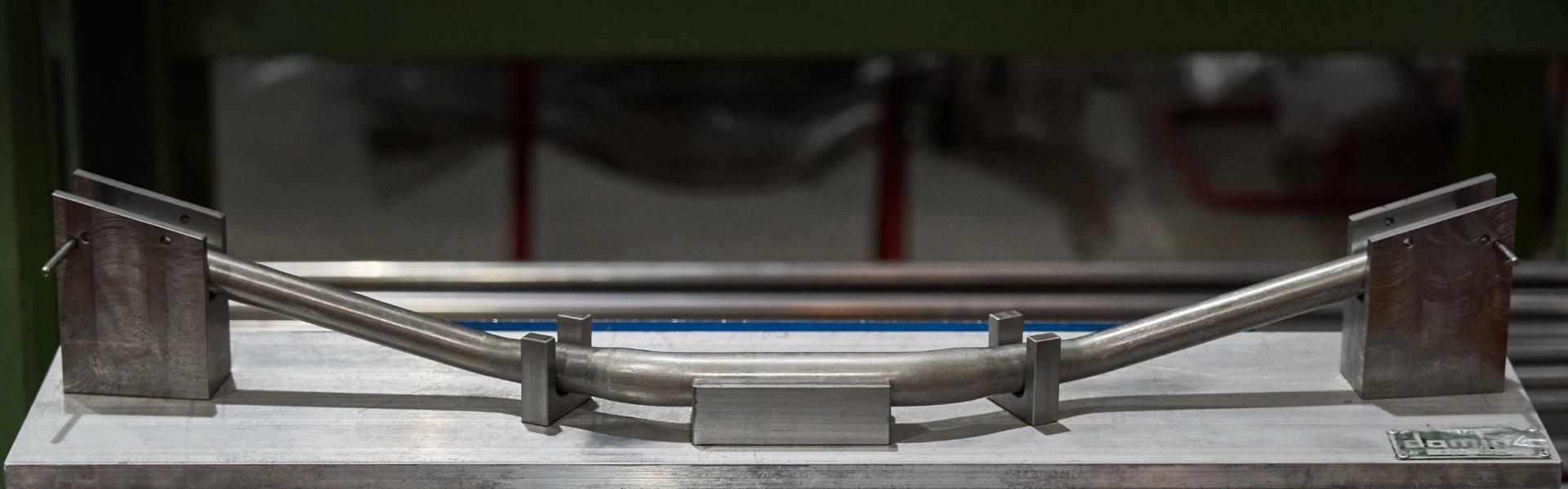
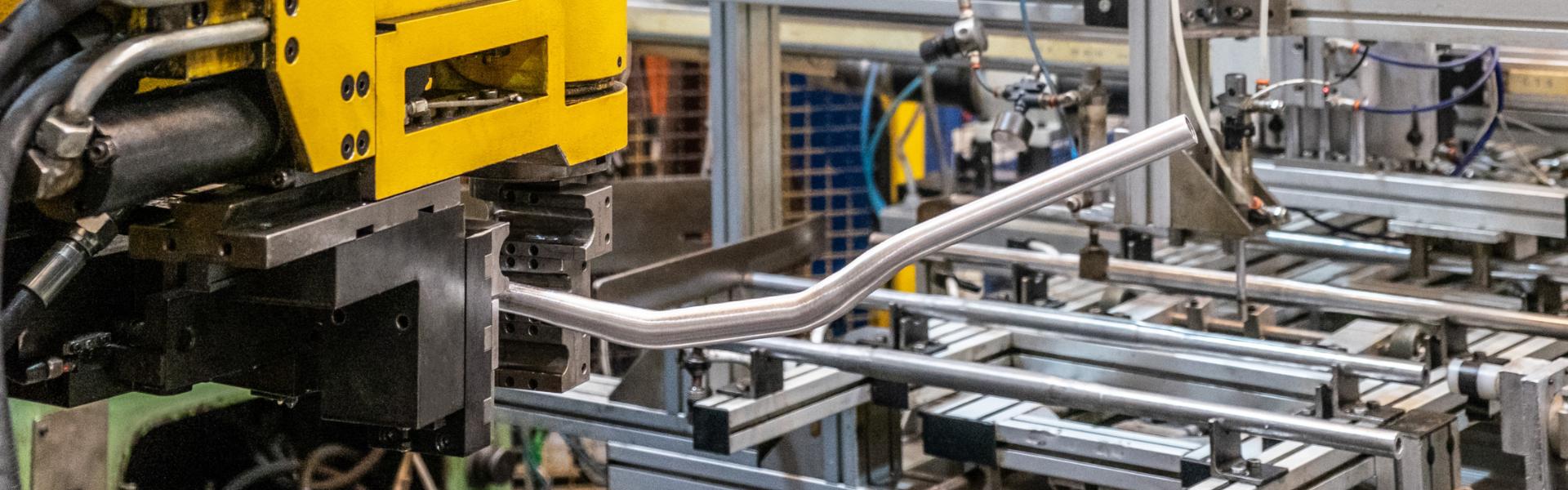
Testing and Validation
Before putting our products to the test on the track and on the road, serious laboratory validation is first carried out in order to confirm their value. A complete internal testing laboratory allows us to perform most of the environmental, structural, reliability and endurance tests required by our own standards, or those of our customers.
A rigorous series of tasks that put the quality of the product and the production and management processes to the test, in order to improve our experience and know-how.
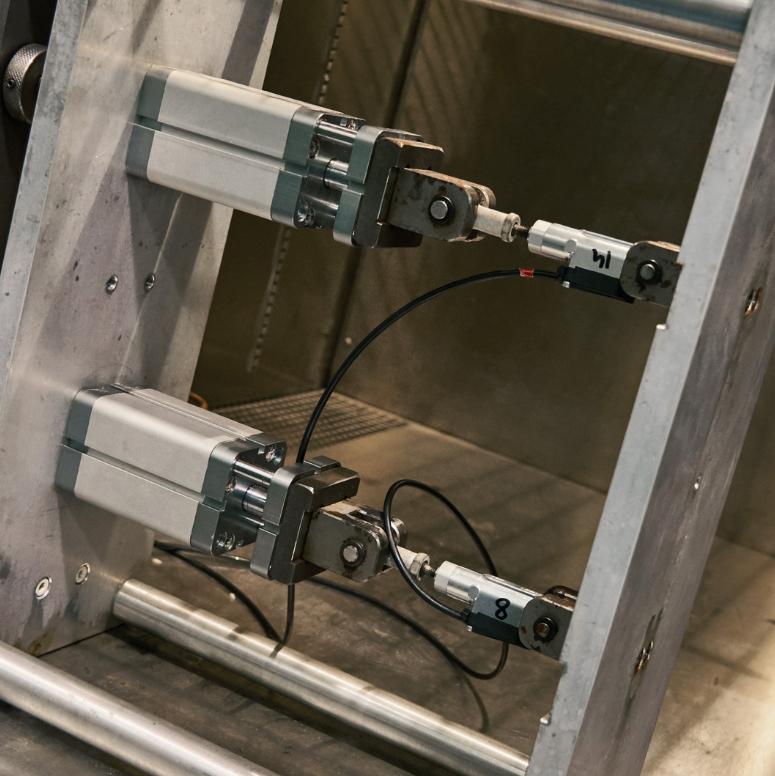
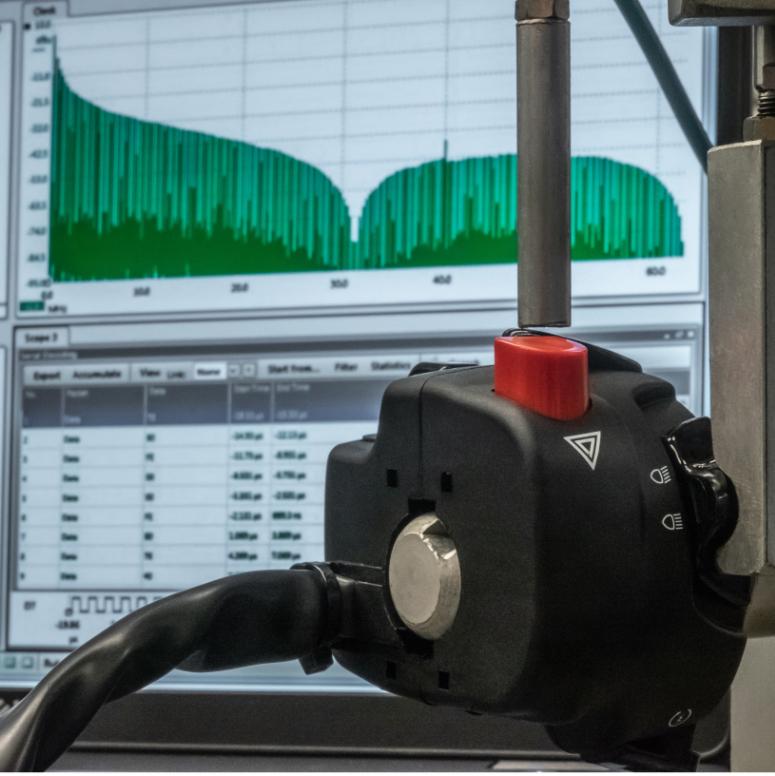
Quality and certifications
We are UNI EN ISO 9001:2015 certified, and have been accredited by the German Ministry of Transport (KBA) for our handlebars through TuV Rheinland.